What is Hot Bar Reflow Soldering?
Hot bar reflow soldering, also known as pulse heat soldering, is a cutting-edge technique used in electronics manufacturing to achieve precise and reliable solder connections. Unlike traditional soldering methods, which rely on manual labor or wave soldering machines, hot bar soldering utilizes localized heating and pressure to join components to a PCB (Printed Circuit Board) with unparalleled accuracy.
Hot Bar Reflow Soldering is a selective soldering process where two pre-fluxed, solder coated parts are heated with a heating element (called a thermode or a hot bar) to a sufficient temperature to melt the solder. After this, the parts are cooled below the solidification temperature to form a permanent electro-mechanical bond.
Flex Carriers and Foil Connectors
Mobile electronics such as telecommunications equipment, as well as the electronics in motor vehicles require increasing packing density and thus arrangement of the circuits in multiple layers. The connection of the layers are favorably produced with flexible circuit carriers and / or foil connectors. These connections are prepared, mostly by Hot Bar Reflow Soldering. For equipping electronic devices (pcb soldering) with digital displays, display drivers on flexible carriers can be used. The connection to the rigid circuit board can be produced by using thermode soldering too. Furthermore the method can be used to join flat cable and foil cable with rigid components like plug connectors and PCBs.
Hot Bar Reflow Soldering Process Explained
For components that require a very precise positioning, Hot Bar Reflow Soldering is the most ideal process. Pulsed heated soldering differs from traditional soldering because the reflow of solder is accomplished using a heating element called a thermode. The thermode is heated and cooled down for each connection. Pressure is applied during the entire cycle including heating, reflow, and cooling. Because pressure is applied during the complete cycle, the process is very suitable for parts that could disconnect during cooling down. By using Hot Bar Reflow Soldering process multiple connections (up to > 100mm length) can be made simultaneously in a single process cycle. Making these connections simultaneously also prevents wires disconnecting while soldering the neighboring one.
Hot Bar Reflow Soldering Benefits
- Fast temperature ramp-up and cool-down
- Closed loop temperature control
- Accurate positioning of the parts
- Multiple connections can be made simultaneously
- Cost effective due to elimination of third component such as connector
- Reliability. By eliminating operator variability, hot bar reflow soldering enhances the reliability and repeatability of solder connections, reducing rework and scrap.
Applications Hot Bar Reflow Soldering
- Consumer Electronics: From smartphones to smartwatches, hot bar reflow soldering ensures the seamless integration of components in consumer electronic devices. You can think of pcb soldering
- Automotive Electronics: In automotive manufacturing, hot bar soldering machines deliver robust solder joints for critical electronic components, ensuring durability and reliability on the road.
- Medical Devices: With stringent quality requirements, the medical device industry relies on hot bar for precise and sterile solder connections in life-saving equipment.
- Aerospace and Defense: From avionics to defense systems, hot bar technology meets the rigorous standards of the aerospace and defense industries, ensuring mission-critical reliability in extreme environments.
Typical Hot Bar Reflow Products
- Connecting flex-foils to Printed Circuit boards
- Small wires
- Small coax cables
- Very light or small components
- Pcb soldering
Pulsed Heating Process Explained
The pulsed heated hot bar reflow (HBR) soldering process is a soldering process where the solder is heated to melt, reflow and solidify.
This process ensures a permanent electro-mechanical joint between two parts. The Hot Bar process allows to heat locally in contrast to reflow ovens. And therefore, ideal for soldering sensitive components and electronic assemblies. The Hot Bar transfers the heat by its footprint and under pressure into the product connection.
Each process cycle this thermode is heated up and cooled down according to a pre-programmed heat profile. In addition to the heating, a controlled force is applied to the parts during the complete cycle, ensuring a mechanical fixation and consistent and accurate alignment of the parts.
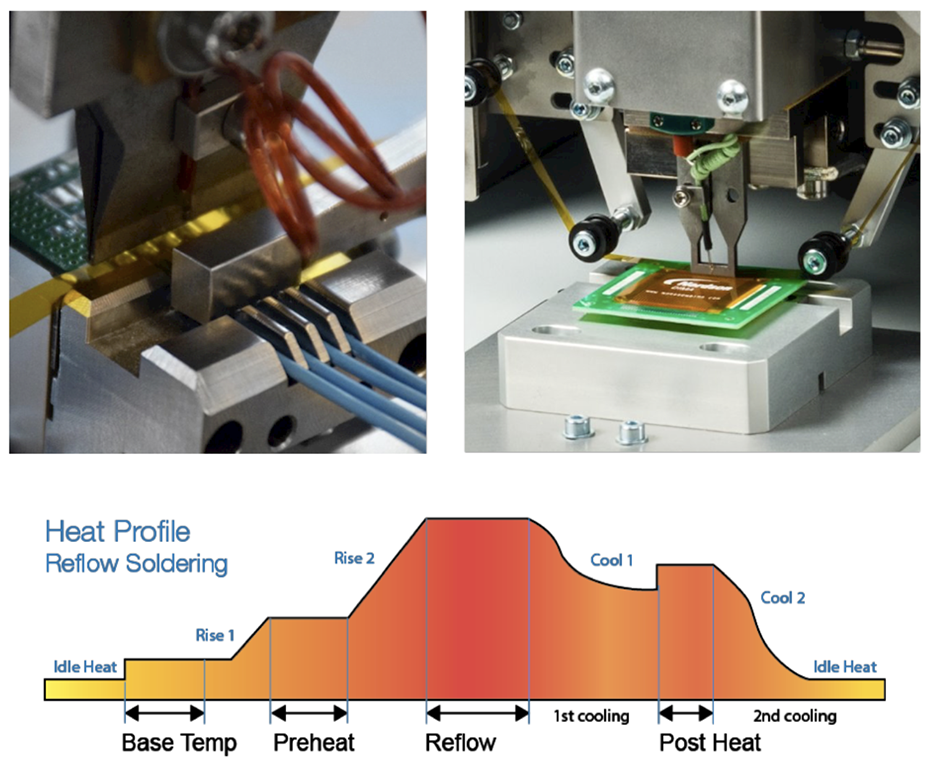
Difference Between Pulsed Heat and Constant Heat
Constant Heat: In constant heat hot bar reflow soldering, a continuous and consistent level of heat is applied to the solder joint throughout the soldering process. This method typically involves maintaining a steady temperature of the heating element for a predetermined period.
Pulsed Heat: In pulsed heat hot bar reflow soldering, heat is applied to the solder joint in short bursts or pulses. This method involves rapidly heating the solder joint to a specific temperature for a brief duration, followed by a rapid cooling phase.
The choice between the two ultimately depends on the specific soldering requirements. For example: component characteristics, and desired solder joint quality. Constant heat may be suitable for some applications. Where simplicity and uniform heating are paramount, while pulsed heat offers greater precision and control for demanding soldering applications. Understanding the differences between these two approaches is crucial for selecting the most appropriate soldering method to achieve optimal results in electronics manufacturing.
Choosing the Right Hot Bar Machine
When selecting a hot bar soldering machine for your manufacturing needs, consider factors such as:
- Temperature Control: Look for machines with precise temperature control capabilities to accommodate various soldering requirements.
- Force and Pressure: Ensure the machine offers adjustable force and pressure settings to optimize solder joint quality.
- Heating Profile (pulsed or constant heat): Evaluate the heating profile of the machine to achieve optimal soldering results for different component types and materials.
- Automation Features: Consider machines with automation features such as vision systems and programmable settings to enhance productivity and consistency.
C-Base
For Heat-Seal Bonding, Reflow soldering, ACF Laminating and Heat-Staking applications.
C-Slide
C-Slide is an ideal product for Heat-Seal Bonding, ACF Laminating process applications and Reflow Soldering. All kind LCD, Flex foil and PCB connections can be made using this system.
C-Turn
Soldering/Bonding Head Modules in different force ranges for optimal process adjustment. Process quality control is guaranteed as never before penetration
Get in touch with us today!
Ready to elevate your soldering capabilities with hot bar reflow technology? Explore our range of hot bar soldering machines and discover the potential for precise, reliable solder connections in your electronics manufacturing processes. Do you have questions regarding our hot bar reflow soldering technology? Don’t hesitate to contact us today.